Non Destructive Testing (NDT ) Activity 1
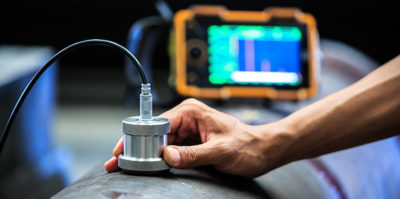
Non Destructive Testing:- Upon completion of oil and gas piping spools, the fabricated pipe spools need to be tested for their integrity to be used in oil and gas mediums. The most common technique for testing these pipe spools is N.D.T. (non-destructive testing). Some of the most common N.D.T. techniques are radiography test (RT), ultrasonic test (UT), magnetic particle test (M.P.T.) and dye penetration test (DPT). Many other advanced N.D.T. methods are available as well, but the above are the most used tests in oil and gas projects. As such, fabrication facilities are not encouraged to perform these tests internally due to conflict of interest. Most of oil and gas clients insist the fabrication contractors must have independent third-party N.D.T. companies to carry out these tests. Thus, N.D.T. activities have become the most important testing activity in the piping fabrication landscape. Many a time, poor performance of these independent N.D.T. companies has led to project delays, additional testing costs and other associated issues in the project. Thus, it is of real importance to understand the various key aspects of N.D.T. scope of activities and its requirements to ensure that these activities are carried out with due diligence. In this section, the most common N.D.T. techniques and the critical points to be looked at for successful N.D.T. work completion are explained in detail.
1 NON-DESTRUCTIVE TESTING (N.D.T.) SUBCONTRACTOR
SELECTION
- N.D.T. subcontractor selection should be done well in advance, before the fabrication works start at the project site. It is not advisable to start working on the N.D.T. subcontractor selection work after the fabrication works have started. This will create accumulation of work and delay in carrying out the required N.D.T. work, including identification and traceability issues.
- A minimum of two subcontractors need to be selected for the project based on the scope of N.D.T. work involved in the project. This is to ensure issues, if any, related to the single N.D.T. subcontractor, such as N.D.T. personnel shortage, payment-related issues, etc.
- The potential N.D.T. subcontractor should have a PETRONAS approved license to carry out NDT work in the project. Care should be taken to check the scope of work mentioned in the PETRONAS license. Absence of ‘PETRONAS’ license and N.D.T. related scope of work in the subcontractor’s current license will lead to rejection by PETRONAS/client representatives. In some cases, PETRONAS license renewals have not been done by the subcontractors, which is again an issue. In a nutshell, the selected subcontractor should possess a valid PETRONAS license with the required N.D.T. scope of work.
- It must be ensured that the subcontractor has the required N.D.T. equipment and manpower. If not, it will lead to uncertainty in terms of continuous engagement and on emergency needs.
- A check and balance on N.D.T. quoted prices versus market prices versus budget available for the project needs to be worked out. This is to avoid cost overruns due to the N.D.T. scope of work. If the budget allocated is less than the anticipated scope of work, the PM must be informed about the possible cost overruns in this area to avoid cost related issues later.
- N.D.T. subcontractors who can cover all the N.D.T. scope of work, such as RT/UT/MT/PT/ P.M.I./hardness testing and P.W.H.T, should be selected. If the ND.T. requirements are very bigger projects, it is always advisable to have subcontractors who can cover the entire scope of work related to N.D.T. This will help to avoid delays and time/effort spent in getting the approval from clients to engage N.D.T. subcontractors.
- N.D.T. subcontractors should be finalized at least one month before the start of actual fabrication work. This is to ensure on-time submission of all the related documents to the client and to facilitate on-time starting of N.D.T. work at the site. Some subcontractors may not provide their N.D.T. procedures if the work order is not issued to them. If fabrication works are started before selection of the subcontractors, it will delay the work.
- The selected subcontractor must submit their company profile, company’s track record, previous experience in similar kind of projects and similar scope of work, etc., to avoid surprises later.
- The duration of employment of the N.D.T. subcontractor must be specified in the work order clearly, and the same must be monitored and controlled to avoid cost overruns.
2 N.D.T. PROCEDURES
- Based on the N.D.T scope of work, the N.D.T. procedures must be identified.
- Identified procedures must be obtained from N.D.T. subcontractors and reviewed internally for their correctness prior to submission to client.
- The identified N.D.T. procedures must be approved by the client prior to start of fabrication work.
- The minimum procedures required are RT/UT/MT/PT/P.M.I./hardness testing and P.W.H.T.
- The selected subcontractor for N.D.T. work must submit the identified procedures within a week of obtaining the work order from the P.C.R..
3 CLIENT APPROVAL FOR N.D.T. PROCEDURES
- Prior to starting N.D.T. work, all the identified N.D.T. procedures must be approved by the client. Comments, if any, by the client during the approval process must be resolved prior to the start of N.D.T. work.
- The client must approve the submitted N.D.T. procedures within two weeks to avoid delay in approvals.
- Close monitoring of N.D.T. approvals by the client is essential for the timely starting of N.D.T. operations in the project.