Cascade Control and Ratio Control
Cascade control and ratio control are two among the several types of control methods used in the industries to automate a process so as to achieve a desired result. They are developments done over the closed loop control process because a closed loop control method is not perfect by itself. If installed properly cascade control and ratio control are able to provide a high degree of accuracy and high degree of control.
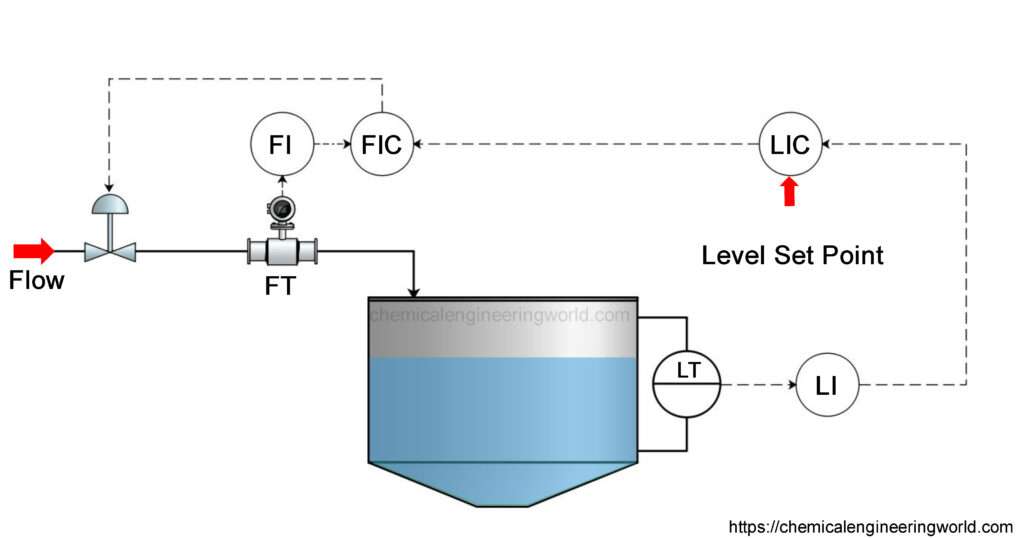
(Cascade Control and Ratio Control)
Often if there are multiple loads in the process then these loads are identified and multiple controllers are assigned to the process in order to control it efficiently. In cascade control, multiple loops are used, one nested in another. The inner loop will minimize the steady state error subject to one type of load and the outer loop will handle a different type of load. This will result in a very stable system overall.
In the following example there are two types of loads, first is that output flow rate may change due to demand of liquid from the tank and second is variations in the input flow rate. The variations in the input flow rate happen due to change in supply pressure. The variation in the input flow rate causes there to be variations in the level of the tank. A flow controller and its corresponding control loop are provided to take care of the variation of the input flow rate. It is the inner loop of the cascade control system. It minimizes the load on the outer loop which is governed by a level controller. The outer loop functions to ensure steady level of liquid in the tank.
The complexity which arises due to implementation of cascade control system is justified only if the inner control loop is at least three times faster than the outer loop.
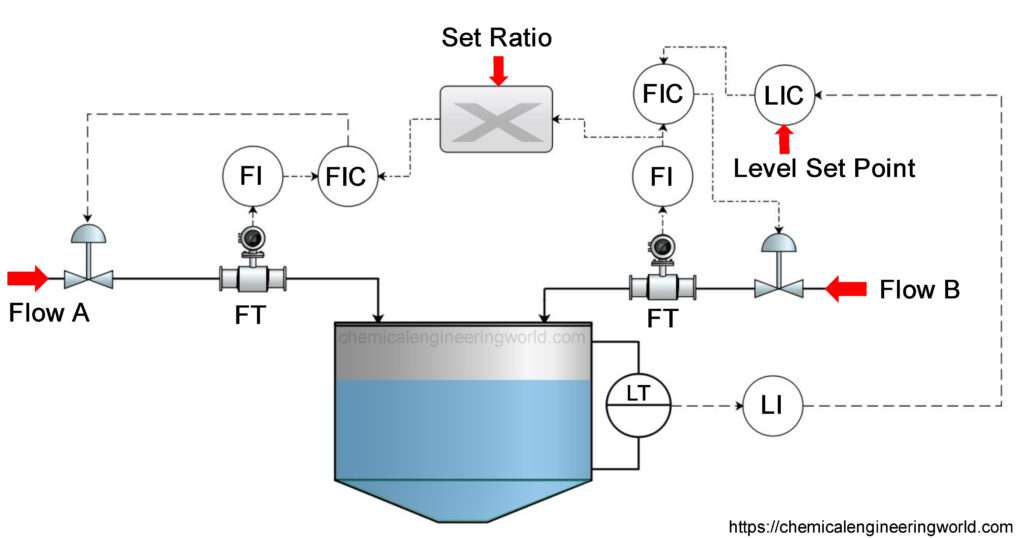
(Cascade Control and Ratio Control)
https://youtu.be/MCf83Ipd-us?t=40
Often it is needed in the process that two variables or two parameters be maintained in a particular ratio such that even if the value of the output changes, the ratio remains a constant. The magnitude of individual variable or a parameter will definitely change if the magnitude of the output changes. An example could be that two semi-liquids could be added in a particular ratio of flow rate to maintain a certain concentration of blend.
In the following example, two fluids are being added to maintain a particular blend. The variable which is measured and controlled is the input flow rates of the fluids. A flow controller is assigned to each fluid; it means each fluid input line has a control loop.
The ratio calculation occurs outside each loop, doing ratio calculation inside the loop will cause problems in the control system because the control system is developed on the concepts of linear algebra and ratio calculation is a non-linear operation. If non-linearity is introduced inside the loops then superposition theorem will no longer apply and the signals cannot be simply added or subtracted. The control process will become very complicated for even simple systems.
Reference:- process-control.com