Rundown Tank Purpose and Working
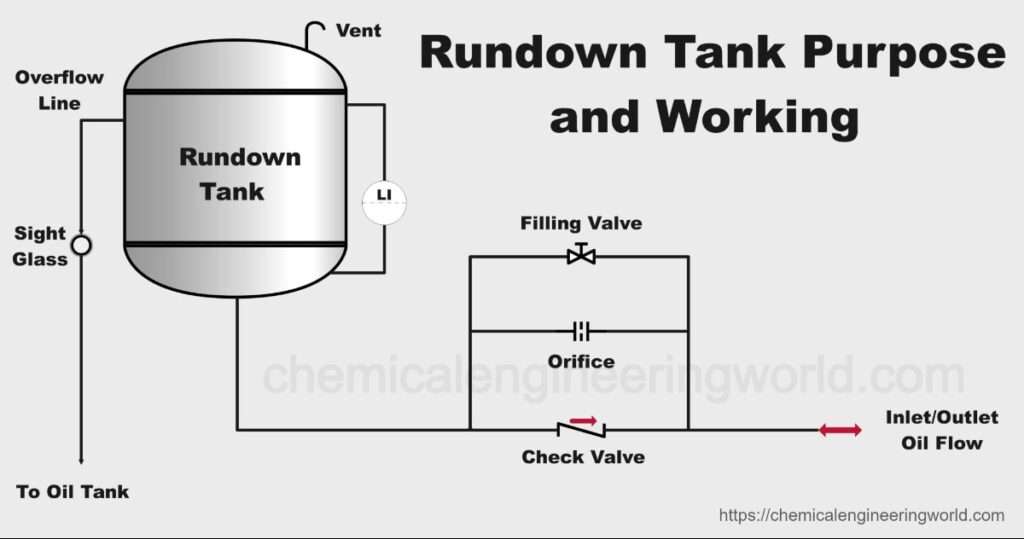
Rundown Tank Purpose and Working
Rundown Tank:
Rundown Tanks Are Simply used for storage of fluid or oil up to a certain height in skid system from the shaft center line of the rotary equipments i.e. Pumps, Compressor whereas pumps can be used for fluid (Liquid & Gas), While Compressor is applicable only for gaseous operation.
Purpose of Rundown Tank:
Rundown Tank is primarily used for the storage of Liquid or oil. It is used as the safety equipment which provides the oil flow to the bearing of various installed rotary equipment i.e. pumps, compressor. Bearings are important machine parts of any rotating equipment with high level of sensitivity even a small damage make them faulty which result in shutdown of the whole plant system.
Commonly used for rundown Tank is in oil – lubrication system which supplies the lube oil to the respective bearing at required flow rate, with respect to pressure & Temperature. Oil is transported to the rotating equipment via skid system network of piping, Valves & Instrument. Electrical & Automation is also used for controlling the system.
It is usually a Skid system that consists of major components such as heat exchanger, rundown cooler, filters, pumps & Driver for these components as well as included in skid system.
Design of the Rundown Tank:
Rundown Tank design on the parameter such as size, capacity. Accurate capacity of rundown tanks provides continuous flow of the oil to the rotating equipment of the skid system under gravity during the coast down time.
Coast down time / Period:
CDT is states as the indication of faulty system; it is defined as the method which is used to assess the mechanical degradation of the rotary equipment.
Operation of the rundown Tank:
Operation procedure for the rundown tank is as follows,
Rundown tank is kept unloaded during the initial startup stage & same philosophy to be followed for the shutdown stage. Level of oil inside the rundown tank is parameter on which rotating equipment start procedure depends; filling of oil to the rundown tank is recommended or provided by the supplement or additional pump.
It is usually involves the cyclic process in oil is in the reservoir is pumped through the supplement or additional pumps, after this process oil is processed to the other component for temperature maintenance in cooler, while for removing any contamination to the filters upto specified sizes (in microns) of oil particles passed through filters, then is forwarded to the header (simple pipeline) for the supply of this oil to the bearing of rotary machinery for proper & efficient operation of the skid system. After these bearing escaped oil through the bearing is moved to the drain. Further it is transported from drain to the Oil reservoir where the process initiated earlier.
Components of Rundown Tank:
A rundown tank assisted with other components with their respective instrument & Valves.
- Vent Connection: For venting & removal of vacuum inside the tank.
- LT (Level Transmitter): for the indication of alarm at low & high level inside the tank.
- Sight Glass: to objectify or visualize the movement & level scenario in the rundown tank.
- Filling Valve: As stated in the operational procedure rundown tank it is opened when initial startup needed Filling valve is kept under normal close position until startup or shutdown case is facilitates.
- Orifice: Orifice provided for lube oil minimum flow from pump discharge to rundown tank.
Check valve: to restrict the oil flow from other component to the rundown tank.
There are so many other instruments & Valves are to provided to the rundown tank system based on the design criteria stated by API in their Standards.
Reference: Sciencedirect, Lubepower