Steam Ejector Working, Types & parts
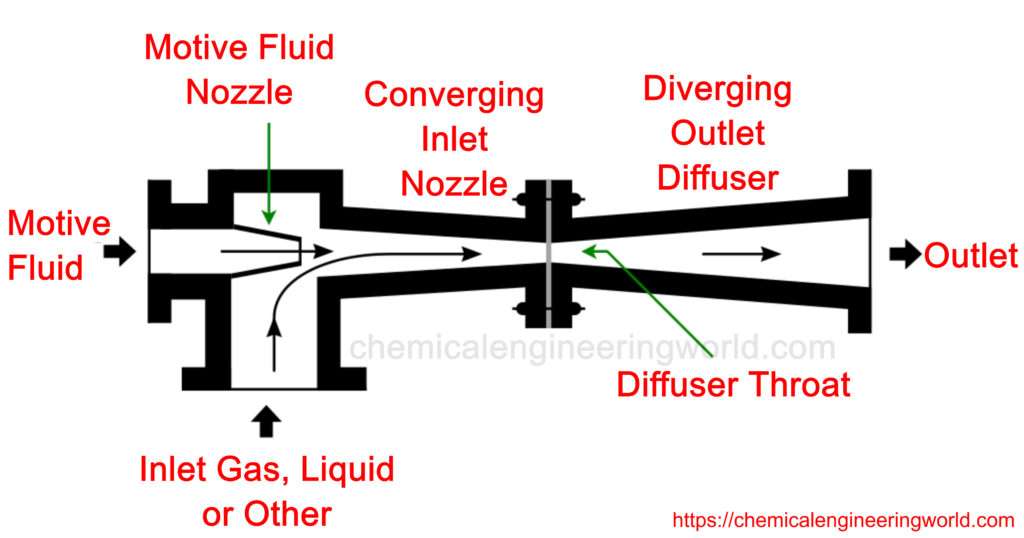
Steam Ejector Working, Types & parts
Working of a Steam Ejector
Ejectors work with an actuating gas which is usually steam. The purpose of the actuating gas is to carry the gas to be evacuated from a container or equipment with it. The evacuation is done for the purpose of creating vacuum conditions. The gas to be evacuated and carried along with steam is called the secondary gas.
The high pressure steam first passes through the steam chamber and enters the suction chamber through nozzle. The nozzle converts the high pressure steam into high velocity stream. The speed of the steam increases quite a lot when it passes through nozzle.
During the working process the actuating gas is expanded from its initial pressure to a pressure equal to that of the secondary fluid. Due to the high velocity of steam through the nozzle, a low pressure region is created in the suction chamber. This causes the secondary gas to move out of the container or equipment and enter into the suction chamber through suction inlet.
Throughout the path of the fluid flow, the actuating gas is decelerated and the secondary gas is accelerated.
After the fluid enters the converging section of the system called the inlet diffuser section the nature of the fluid flow corresponds to supersonic flow. The characteristics of the supersonic flow are that when cross-sectional area decreases then the velocity of fluid also decreases and the pressure increases.
The throat section is where the transition of the nature of flow from supersonic to subsonic takes place.
The nature of flow in the outlet diffuser section is subsonic. Since the outlet diffuser is the diverging part, the characteristics of a subsonic flow can be described as when the cross-sectional area increases then the velocity decreases and the pressure increases.
Steam Ejector Uses
Steam ejectors are equipments which are primarily used in process, food, steel, petrochemical etc industries to create vacuum conditions. They can also be operated as transfer and mixing pumps. They can be employed for operations which involve filtration, distillation, absorption, mixing, freeze drying, dehydrating, degassing etc.
Steam ejectors are quite rugged and simple in construction and also quite simple to operate. They can handle large volumes of gases in relatively smaller designs and also the cost of maintenance is low.
Some of the advantages that the steam ejectors have over conventional vacuum pumps are that steam ejectors have no moving parts at all, it means there is no problem of wear and tear within the equipment. Steam ejectors can be made of practically any workable material hence specific erosion resistant material can be chosen and they can also be coated with a corrosion resistant material.
Steam ejectors have capability of performing very well and creating vacuum conditions at high efficiencies.
Steam Ejector parts
- Steam Chest
- Suction Chamber
- Steam Nozzle
- Inlet Diffuser
- Throat Section
- Outlet Diffuser
Steam Chest:
It is the section through which high connection motive steam enters from appropriate surrounding to the steam ejector system.
Suction Chamber:
It is the next section in which steam enters. Suction Chamber houses nozzles, suction inlet and mouth of the diffuser inlet. The suction inlet corresponds from where the gas to be evacuated from a container or an equipment moves out of the container or equipment and enters suction chamber.
Steam Nozzle:
When steam flows into the nozzle the pressure energy of steam gets converted into kinetic energy. Nozzle is capable of driving steam to high velocities.
Inlet Diffuser:
It is the converging part which is attached to the suction chamber. The mixing of the steam and the gas to be evacuated gets completed in this section. The nature of fluid flow in the inlet diffuser section is supersonic.
Throat Section:
It is a section of constant diameter between the inlet diffuser section and outlet diffuser section.
Outlet Diffuser:
It is the diverging part of the system where the steam enters after passing through the throat section. The nature of fluid flow in this section is subsonic. Most of the kinetic energy gets reconverted to pressure energy in this section.
Types of Steam Ejector
The purpose of staging ejectors is that very large range of suction pressures can be obtained. The range can go from atmospheric to pressures whose magnitude is in microns of mercury absolute. If more than a single stage of steam ejectors is used for some operation then it is advantageous to condense steam before passing it to succeeding stages. This reduces the steam consumption and makes the system more efficient to operate.
Single-Stage Steam Ejectors:
They cover a range of suction pressure from 30 mm Hg absolute to atmospheric pressure. The discharge pressure is near atmospheric pressure. The design of the steam ejector can be optimized so that the steam consumption is minimized.
Two-Stage Steam Ejectors:
They cover a range of suction pressure of 3 mm Hg absolute to 130 mm Hg absolute. The first stage is called low pressure vacuum steam ejector and the second stage is called high vacuum steam ejector. The first stages takes pressure to some intermediate pressure which acts as an optimum input to the second stage.
Three-Stage Steam Ejectors:
They cover a range from 0.8 mm Hg to 25 mm Hg absolute. A three stage system contains a primary booster along with the low and high vacuum steam ejectors. The low vacuum ejector brings the pressure to an intermediate pressure. The high vacuum steam ejector takes the pressure to another low intermediate value and finally the booster takes the pressure to final condition.
More-Stages Steam Ejectors:
As the number of stages increases, the number of boosters employed in the system also increases. Four-Stage Steam Ejector covers the range from 75 microns Hg to 4 mm Hg absolute. Five-Stage Steam Ejectors covers the range from 10 microns Hg to 0.4 mm Hg absolute. Six-Stage Steam Ejectors cover the range from 3 microns Hg to 0.1 mm Hg absolute.
Reference:- venturipumps, graham-mf