Cement Manufacturing Process
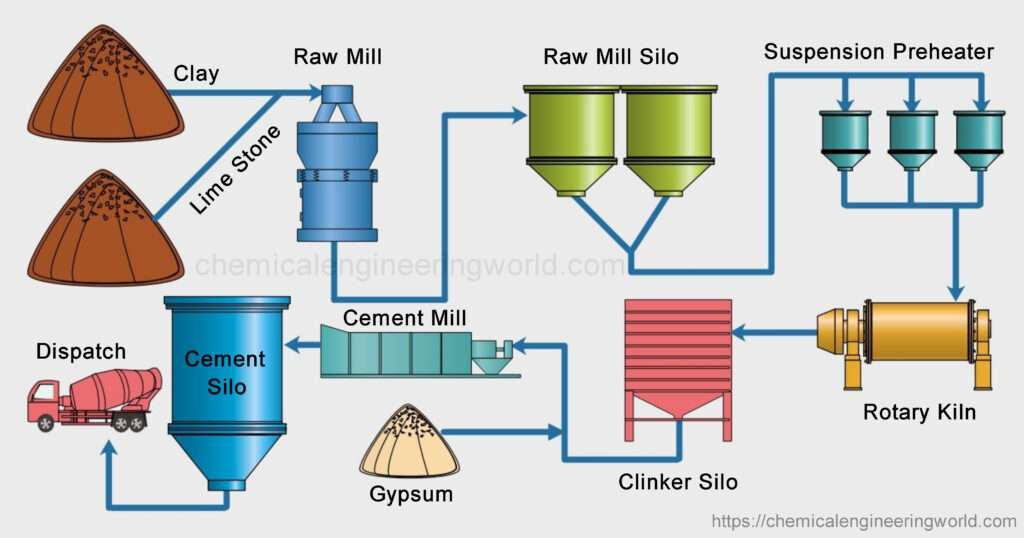
Cement Manufacturing Process
Cement Manufacturing Process
Cement is a material which is used to bind other materials together. Binding means it has an effect of gluing the substances together due to cohesive and adhesive action and then hardens and sets in order to become permanent. Cement is usually not used on its own; it is mixed with other materials called aggregates to produce a combined material of desired properties.
When it is mixed with sand, gravel then concrete is produced. If it is mixed with fine aggregates then it produces mortar. Cements are prepared by materials which have a high amount of calcium or aluminium and silicon. Calcium containing materials are called calcareous materials and aluminium and silicon containing materials are called argillaceous materials. Cement is used for constructing buildings, dams, roads, bridges etc.
Depending on the ability of the cement to set in presence of water it is characterized as Hydraulic cement and Non-hydraulic cement:
Non-Hydraulic Cement:
These are cements which require dry conditions in order to set and harden. They lose their efficiency and durability in presence of water. It sets as it dries and reacts with carbon dioxide in air. After setting it is resistant to chemical attacks.
Hydraulic Cement:
These are cements which can set even if it’s surrounded by any amount of water. In such cements, the cement reacts with aggregates to form mineral hydrates which are insoluble in water. The water can protect the cement and the aggregate from chemical attacks this helping it set and harden and become very durable. An example of this type is Portland Cement.
The manufacturing of cement generally involves four steps:
- Mixing
- Burning
- Grinding
- Storage
Mixing:
The mixing of raw materials can be done either with dry process or wet process.
In dry process the calcareous and argillaceous materials are grinded to the required size and then they are mixed in required proportions and stored in silos, ready to be fed into rotary kiln.
In wet process the calcareous and argillaceous materials are grinded to required size and stored in separately silos. Before the argillaceous materials are stored it is first washed with water. Both the materials are then channeled to mill equipment where they are intimately mixed in desired proportions to form a paste. This paste is then stored in a silo for further processing.
Burning:
The process of burning is carried out in rotary kiln and the rotary kiln is lined with refractory bricks. The prepared mixture stored in the silo is fed into the rotary kiln from upper side and a burning fuel is fed from the lower side of the rotary kiln in order to produce hot flame. The fuel can be oil or powdered coal or it even can be hot gases.
There is a temperature gradient inside the rotary kiln with the lowest temperature being at the upper side and the highest temperature being at the lower side. There is a countercurrent motion between the feed mixture and the burning fuel. Due to the slow rotation of the rotary kiln the temperature of the feed mixture rises gradually as it moves from the upper end to the lower end of the rotary kiln.
The rotary kiln is divided in to three parts; the upper part, the central part and the lower part. The processes ongoing in each of the parts are:
Upper Part:
It is maintained at 400°C. Water or moisture in the feed mixture is evaporated.
Central Part:
The temperatures are around 1000°C. This part is also known as calcination zone because lime stone decomposes in this part. Calcium carbonate decomposes to form calcium oxide and carbon oxide. After the carbon dioxide escapes remaining material forms small lumps called nodules.
Lower Part:
The temperatures in this part are between 1500-1700°C. This part is also known as clinkering zone. The calcareous and argillaceous materials react to form calcium silicates and calcium aluminates. The aluminates and silicates fuse together to form small and hard stones known as clinkers.
Grinding:
The clinkers which are output from the rotary kiln are very hot hence they are first cooled by air in a countercurrent fashion. The clinkers are of size of about 5-10 mm. They are fed to grinders in order to grind them to reduce their sizes. The clinkers are fed into ball mill or tube mill along with powdered gypsum.
The gypsum acts as a regarding agent so that the resulting cement does not set quickly when it comes in contact with water. The mixture fed for grinding contains tricalcium aluminates which are soluble in water. Gypsum reacts with them to produce tricalcium sulfoaluminates which is insoluble in water. They retard the rate of setting of cement thus giving time for concrete placing.
Storage:
The grinded cement is then stored in silos. They are stored in 50 kg bags and then shipped and marketed as container loads. Clinkers can also be marketed and sold as per the requirement of the buyer.