Reactive Distillation
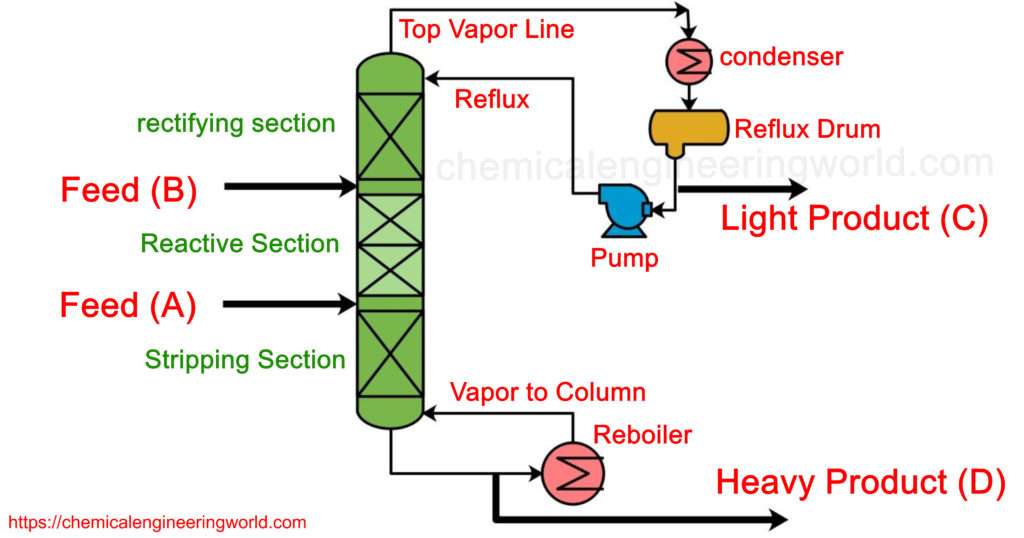
Reactive Distillation is a type of process operation which is a combination of a chemical reactor and a distillation column. It means the feed are mixed in the column and the nature of the feed is such that they are reactive hence due to the chemical reaction the products are formed and the nature of product is usually such that they are easily separable from each other and the feed reactants themselves. There are various trays installed in the column on which the formed products get separated.
Since there are numerous types of chemical reactions, the type and nature of reactive distillation columns are also numerous. An ideal case in which reactive distillation is beneficially used is when the relative volatilities of the products formed lie in the extreme of all the compounds present in the column.
Consider the following reversible chemical reaction:
The reactants A and B react to form products B and D. In the ideal case the general distribution of the compounds with respect to the relative volatilities is given by:
The above statement means that the relative volatilities of the products C and D lies in the extreme and the relative volatilities of the reactants A and B are intermediate with respect to the products. Compound C is the lightest, Compound A is lighter than B, Compound B is lighter than D and Compound D is the heaviest.
In this Ideal case, the reactant A is lighter than B hence it is fed at the lower section of the column but not at the very bottom and reactant B is fed in to the upper section of the column but not at the very top. The section between these two feeding points is called the reactive section.
As component A flows up the column, it reacts with the descending B and very light product C is produced, it gets quickly removed from the reaction section
along with the vapours. A very heavy product D is also produced and it also gets quickly removed from the section along with the down flowing liquids.
The section above the tray where reactant B is fed is called a rectifying section. The feature of this section is that very light product C separates and goes in to vapour phase effectively such that the distillate formed is quite pure in product C.
The section below the tray where the reactant A is fed is called the stripping section. The defining feature in the stripping section is that the liquid gets richer in product D such that the bottoms product obtained contains product D mostly.
The reflux ratio and the reboiler heat input can be manipulated to control product purities.
Limitations of Reactive Distillation
- The relative volatilities of the compounds should be such that most of the reactants must get consumed in the reaction zone itself and products must pass through rectifying and stripping section to reach the distillate and bottoms. Not all Chemical reactions follow this hence it becomes more challenging to control the process if the case is otherwise.
- The temperature required for optimum reaction and the temperature required for optimum separation are often different. Since the entire column operates at a single pressure the temperatures are fixed by tray composition, a column should be properly designed so that no mismatch occurs in temperature.
- If the reactions are too slow then the size of reaction section increases, it means the number of trays increases. A very slow reaction requires very tall columns.