Three Phase Separator
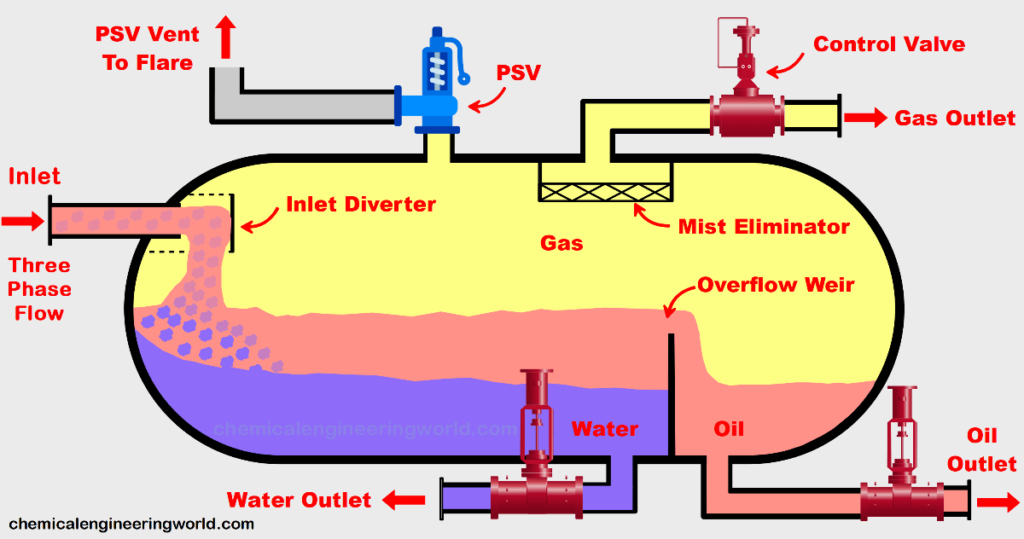
Three Phase Separator
Introduction:-
A separator is a gadget used to separate or isolate a well stream mixture of oil/gas/water into its constituents. For instance, a gas-liquid separator is utilized to extract and collect entrained fluids from natural gas streams. As a general rule, a straight length of piping is required upstream of a separator to ensure or guarantee that the flow is completely evolved and uniform prior to entering the separator. This straight length permits the fluid to balance out and diminishes turbulence and swirl, which can adversely affect the separation performance of the separator.
What is a three-phase separator?
Three-phase separators are a fundamental tool in assisting with maintaining safety, productivity levels as well as the quality of the product in the oil and gas industry. They help by lessening the requirement for any kind of repair and maintenance. This is an essential benefit to any organization that wants to maximize profits. The three-phase separator is an essential component of the petroleum production system, which is utilized to separate reservoir fluid from oil, gas, and water. Then these separated flows are shipped or moved downstream for further processing.
As a general rule, a mixed fluid can be viewed as a small amount of liquid A or/and gas B dispersed in a large amount of fluid C. In this situation, the dispersed liquid A or gas B is known as the dispersed phase, while the large continuous fluid C is known as the continuous phase. For gas-liquid separation, it is at some point vital to dispose of tiny drops of liquid A and C from a large amount of gas B, where gas B is the continuous or persistent phase, and fluid A and C are the dispersed stages. At the point when just a single liquid and gas is considered for separation, it is known as a two-phase separator or a liquid-gas separator.
The fundamental principle of a separator is gravity separation. By utilizing the density difference of various phase states, the drop can settle or float freely under the combined force of gravity, lightness, fluid resistance, and intermolecular forces. It has great pertinence for both laminar and turbulent flows.
Why do you need to use a three-phase separator?
Any organization that works within the oil and gas sector wants to maximize profits while maintaining an excellent safety record. Utilizing a three-phase separator assists in making this happen by eliminating guesswork from the operation and permitting production wells and frac throwback processes to be checked.
These separators are not difficult to transport so they can be utilized out in the field easily. This assists with maintaining an organization’s profits and its phenomenal record for safety. Both of these are imperative factors in the endurance and growth of any company.
What are types of three-phase separator?
1. Horizontal three-phase separator with an overflow weir:-
In a horizontal three-phase separator, fluid or liquid enters the vessel through an inlet and promptly hits an inlet diverter. The sudden impact and change of direction assist in releasing the gas by breaking the surface tension of the fluid. In the liquid collection section of the vessel, the oil separates and frames a layer above the water. A point of interface level controller maintains the oil-water level. This controller signals a dump valve to set water free from the vessel depending on the situation to maintain the oil-water interface level.
The oil spills over the top of the weir, and afterward a level controller or regulator, which operates the oil dump valve, controls its level. A point of interface level controller or regulator additionally senses the height of the oil-water interface. This regulator or controller signals another dump valve to release as much water from the vessel as is expected to stay aware of the oil-water interface at the per-determined height.
In the meantime, gas ascends to the top of the separator. It flows or streams in a horizontal manner and further exits through a fog extractor to a high pressure control valve, which further keeps up with constant vessel pressure.
2. Horizontal three-phase separator with oil bucket and water weir:-
In a horizontal three-phase separator with an oil bucket or pail and water weir, the vessel doesn’t need an active interface controller or regulator. As the oil separates on top of the water it spouts out over the weir plate and into the oil container. The oil level in the bucket or pail is obliged by a level controller or regulator passing a signal to the oil dump valve. The water flows under the oil bucket and over the water weir where it is constrained by the water level controller and dump valve.
3. Vertical 3-phase separator with interface control:-
In a vertical 3-phase separator with interface control, the emulsion enters the vessel and promptly stirs things up around the inlet diverter plate, separating the main part of the gas upon passage. The inlet diverter likewise assists with controlling the emulsion flowing into the vessel by directing it down at the side wall, limiting disturbances to the fluid.
The emulsion encounters a splash guard to additionally limit agitation when we go lower in the vessel. This baffle is open and allows the emulsion to flow descending while simultaneously protecting direct interaction with the point of interaction level controller or regulator to thwart a false reading of the liquid level.
As the oil separates the point of interaction is not entirely set in stone. The point of interaction or connection level controller or regulator will open the water dump valve when the point of interaction level ascents.
This oil level is moreover constrained by a liquid level controller or regulator, which will open the oil dump valve when the oil level increases. The gas goes to the most elevated point of the vessel through a fog extractor and a back pressure control valve that maintains steady or consistent vessel pressure.
4. Vertical 3-phase separator with a downcomer and spreader:-
In a vertical 3-phase separator with a downcomer and spreader, the flow enters the vessel through the inlet and is promptly met by an inlet diverter to help with isolating the bulk of the gas.
A downcomer sends the liquid through the oil-water interface point to hold back from disturbing the fluid in the vessel.
The downcomer outlet, or spreader, is situated at the oil-water interface. Water, being heavier than oil, will separate and settle to the lower part of the vessel. The point of interface level controller or regulator will open the water dump valve when the point of interaction level climbs. The lighter oil will separate and lay on top of the water. The weir height decides the oil level. Oil flows or streams over the weir and further into the oil bucket or pail. This oil level in the bucket is then constrained by a level controller, which opens the oil dump valve when the level increases. A chimney stack equalizes gas pressure between the lower part of the vessel and the gas segment.
What are the benefits of 3 Phase separator?
Beneath we will take a look at the various benefits of a three-phase separator:
1. Accurate Measurement and Allocation of Production Fluids:-
The exact estimation and allocation of production fluids are essential in improving production levels for oil and gas operations. By using a 3 phase separator, your organization can really monitor and control the flow rates of extricated oil, gas, and water, which ensures that your project remains beneficial and productive.
2. Mitigating Environmental Impact: –
The oil and gas sector is continually under critical examination by ecological regulators because of the potential impacts on the environment. By implementing a 3 phase separator, you can ensure that hazardous gases and pollutants are captured and contained during the separation process, decreasing the probability of ecological contamination and resistance to administrative necessities.
3. Reducing Pipeline and Storage Facility Stress:-
pipelines and storage facilities from unanticipated stress and degradation, in this way extending their operational life expectancy. With an appropriately working 3-phase separator in place, you can decrease the risk of pipeline and storage facility damages, staying away from spontaneous downtime and expensive repairs.
4. Minimizing Emissions and Safety Risks:-
The oil and gas industry is innately dangerous, making it crucial for organizations to do everything possible to mitigate safety risks on-site. A well-designed 3-phase separator assists with minimizing the emission of harmful gases, therefore diminishing the risk of explosions and other safety perils in the working environment.
What factors do you need to consider while choosing the right three-phase separator?
Choosing the ideal three-phase separator for your particular project requirements includes thinking about a few variables. A portion of these essential factors are mentioned below:-
1. Flow Rates:
The flow rates of oil, gas, and water extracted from your well can significantly impact the performance and efficiency of your chosen separator. Make sure to clearly lay out your project’s flow rates and select a separator capable for taking care of these volumes.
2. Pressure and Temperature Ranges:
Various separators are designed to function ideally within specific pressure and temperature ranges. Prior to choosing your separator, ensure that it is viable with your unique operating conditions.
3. Size and Installation Requirements:
Contingent upon your project’s accessible space and infrastructure, settling on a horizontal or vertical separator might be more appropriate. Consider these factors while deciding on the type and size of your separator.
4. Cost and Maintenance:
Similarly as with any piece of equipment, it’s essential to consider both the initial forthright expenses and ongoing maintenance costs related to your chosen separator. Make sure to consider these costs in your project financial plan.
How Does a Three-Phase Separator Work?
The purpose or motivation behind a 3-phase separator, or free-water knockout (FWKO) is to extract the oil from different elements in raw petroleum like air, residue, and particularly water, which can cause corrosion or blockages due to forming tight emulsions. Crude oil enters an inlet and hits an inlet diverter, which separates or isolates the solids from the gasses. The liquid is then further collected in the vessel and internal components use gravity to separate the oil from the water. This process requires exceptionally exact measurement of the gas and oil proportion and control of the liquid flow, making it a great representation of a process control and instrumentation application.
Conclusion:-
Natural gas operators use a few devices to purify well streams in offshore and onshore facilities prior to carrying out oil and gas measurement and sale. Dehydrating natural gas assists with forestalling a few issues that occur in storage and transportation, for example, corrosion of storage vessels, errors in the metering of gas flow, and the presence of unwanted compounds within the product. 3-phase separators are generally utilized for gas-liquid or oil-gas separation at processing facilities. The adoption of 3 phase separators in oil and gas operations has turned into a critical factor in ensuring the success safety, and efficiency of your projects. These innovative gadgets are revolutionizing the way that organizations approach their operations by providing accurate measurement and allocation of production fluids, mitigating ecological effects, reducing pipeline and storage facility stress, and limiting emissions and safety risks.
Source:- hcpetroleum, tigersafetyrentals, kimray, forain, ifsolutions